Gulftainer
Boomi helps the international ports and logistics solution provider reduce business process creation time by 40% with reusable components that dramatically optimize operations.
Business goals
Gulftainer wanted to address the key business, supply chain, and logistical issues facing ports. In 2020, the company decided to create a one-stop shop for customers with cargo in a Gulftainer port.
Since Gulftainer handled all cargo-related activity, this integrated service offering would combine the best features of 3PL and 4PL providers.
Integration Challenges
The company could not rely on its legacy enterprise service bus (ESB) middleware with point-to-point integrations, as it lacked scalability. Inputting information from six critical external systems into the core SAP platform was time-consuming and had to be constantly monitored.
Moreover, the point-to-point connections weren’t reusable and required significant ongoing maintenance.
How Boomi Helped
Boomi proved to be the best fit in Gulftainer’s evaluation metrics of integration platforms in the marketplace. With Boomi, Gulftainer deploys bi-directional data flows, which are essential to keeping critical systems synchronized with accurate, up-to-date information.
Moreover, the reusable components within the Boomi Enterprise Platform help slash development costs, and provide the flexibility to meet future growth requirements.
Results
Gulftainer achieved real-time visibility throughout its port operations. The IT team has dramatically improved productivity with the Boomi Enterprise Platform. Results include:
- 75% reduction in process monitoring, which ensured the proper posting of invoices
- 40% reduction in the time required to deploy a new process
- 30-to-40% faster turnaround using existing components to create new process interfaces
- 50% reduction in troubleshooting
Gulftainer also now has a simplified technology landscape, going from 27 interfaces to just 12.
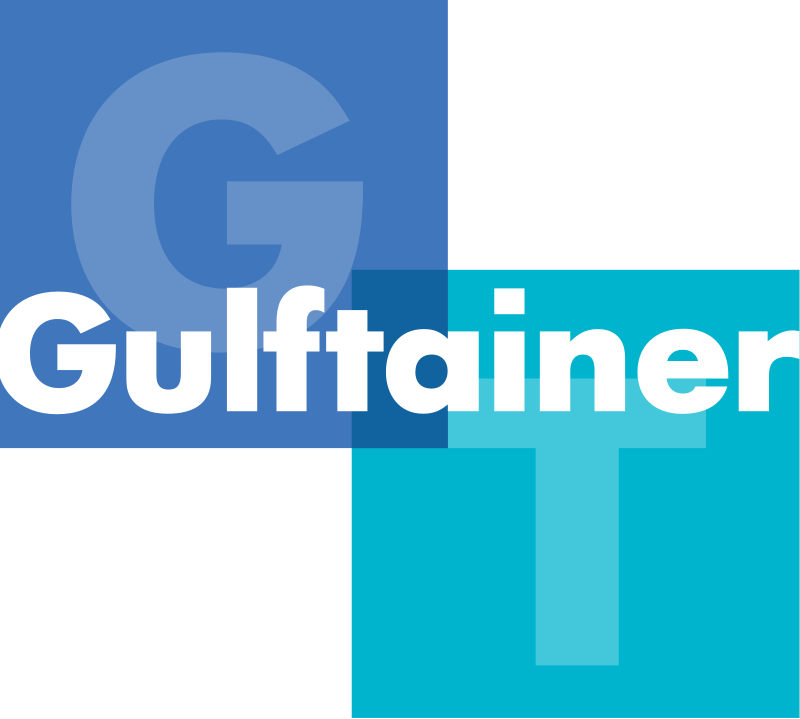